Why Do You Need to Autozero a Melt Pressure Transducer?
- Bob
- Mar 22
- 2 min read
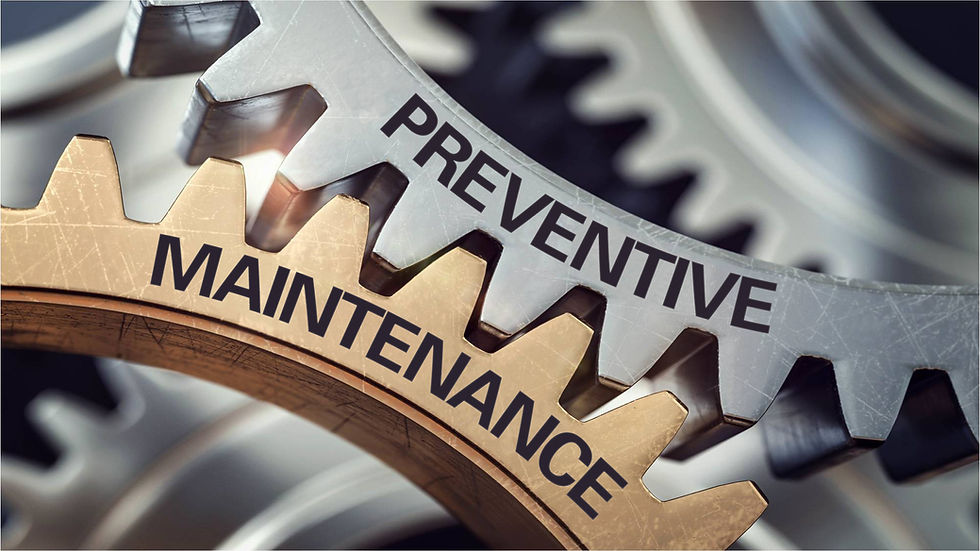
Autozeroing a melt pressure transducer ensures accurate pressure readings by eliminating any signal offset when no pressure is applied. Over time, environmental conditions, electrical drift, or mechanical factors can cause small deviations in the baseline output, leading to inaccurate measurements. Autozeroing corrects these offsets and ensures precise pressure readings.
How Does Autozeroing Work?
Most melt pressure transducers generate a small electrical signal (usually in mV or mA) even when no pressure is applied. Autozeroing electronically resets the output signal to a true zero reference point, effectively removing any small inherent error or drift in the measurement system.
Steps to Autozero a Pressure Transducer:
Ensure the System is at Zero Pressure:
Make sure the system is not pressurized.
Remove any residual material or ensure the transducer is in a relaxed, unpressurized state.
Allow the Transducer to Reach Operating Temperature:
If the transducer is used in a heated environment (such as in extrusion or injection molding), let it stabilize at its operating temperature before zeroing.
Disconnect External Load or Pressure Source (if applicable):
Ensure no mechanical forces or pressure sources are acting on the transducer.
Activate the Autozero Function:
This may involve pressing an "Autozero" button on the transducer or associated instrumentation.
In some systems, autozeroing is performed via a software command.
Verify the Output Signal:
After autozeroing, check the output signal to confirm it reads zero (e.g., 0 mV, 4 mA, or 0 psi/bar).
If the signal is still incorrect, ensure proper installation and repeat the process.
Resume Normal Operation:
Once autozeroing is complete, reintroduce pressure and verify the transducer functions correctly.
By performing this procedure, you ensure your melt pressure transducer provides reliable and accurate pressure readings, reducing the likelihood of errors in your process. If issues continue, please contact our NoNonSensors support group. (We are happy to trouble shoot a wide range of other brands as well!)
Comments