Most Common Melt Pressure Transducer Failure Reasons
- Bob
- Dec 27, 2024
- 2 min read
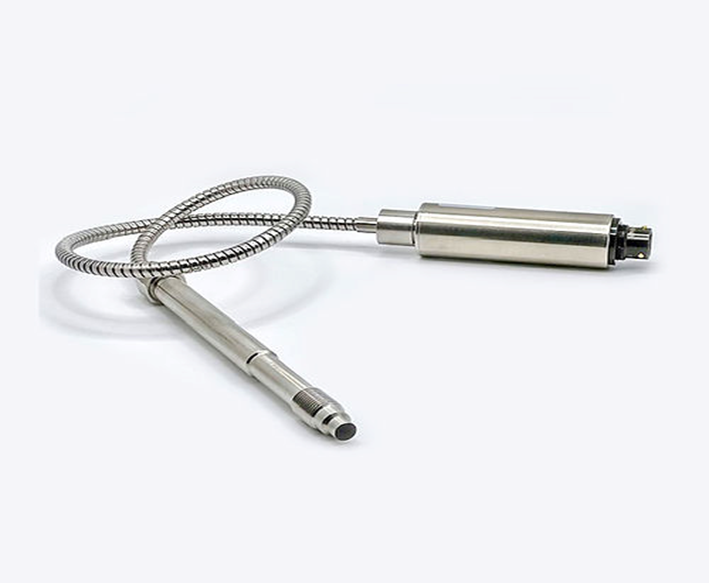
Melt pressure transducers, widely used in applications such as plastic extrusion and injection molding, can fail for several reasons. Here are the most common failure causes:
1. Overpressure
Cause: Subjecting the transducer to pressures beyond its rated capacity.
Effect: Damage to the sensing diaphragm, leading to inaccurate readings or complete failure.
Prevention: Use a transducer with an appropriate pressure rating and install overpressure protection mechanisms.
2. Excessive Temperature
Cause: Exposure to temperatures beyond the transducer's specified range, often due to improper cooling or heat transfer from the process.
Effect: Degradation of internal components, such as the sensing element or insulation, leading to loss of function.
Prevention: Ensure proper thermal insulation, cooling, and adherence to temperature specifications.
3. Physical Damage
Cause: Mishandling during installation or maintenance, such as overtightening, bending, or dropping the transducer.
Effect: Structural damage to the body or diaphragm.
Prevention: Handle the transducer carefully and use appropriate tools and torque specifications during installation.
4. Chemical Corrosion
Cause: Exposure to aggressive chemicals or abrasive materials in the melt stream that attack the diaphragm or sensor housing.
Effect: Corrosion or erosion of the diaphragm, affecting accuracy or leading to failure.
Prevention: Use transducers made from corrosion-resistant materials suited to the application.
5. Electrical Issues
Cause: Voltage spikes, improper wiring, or poor grounding.
Effect: Damage to the transducer's internal electronics, resulting in erratic signals or no output.
Prevention: Install surge protectors, follow correct wiring practices, and ensure proper grounding.
6. Sensor Drift
Cause: Long-term exposure to high pressures and temperatures can cause material fatigue in the sensing element.
Effect: Gradual loss of accuracy and reliability in readings.
Prevention: Regular calibration and periodic replacement based on the manufacturer's recommendations.
7. Contamination
Cause: Accumulation of process material or debris on the diaphragm.
Effect: Impaired pressure measurement due to blocked sensing orifices or changes in diaphragm sensitivity.
Prevention: Regular cleaning and ensuring process material compatibility.
8. Installation Errors
Cause: Improper mounting, such as misaligned threads or excessive tightening torque.
Effect: Damage to threads, seals, or the diaphragm, leading to leakage or failure.
Prevention: Follow manufacturer guidelines for proper installation.
9. Vibration or Mechanical Stress
Cause: Prolonged exposure to vibrations or mechanical forces in the operating environment.
Effect: Internal component damage or loose connections.
Prevention: Use vibration isolation mounts or secure the transducer properly.
10. Age and Wear
Cause: Prolonged use under harsh operating conditions.
Effect: Gradual degradation of sensor components, leading to failure over time.
Prevention: Routine maintenance, inspection, and timely replacement of aging transducers.
Comentários