Common Installation Concerns for Melt Pressure Transducers in Extruders
- Bob
- Feb 25
- 2 min read
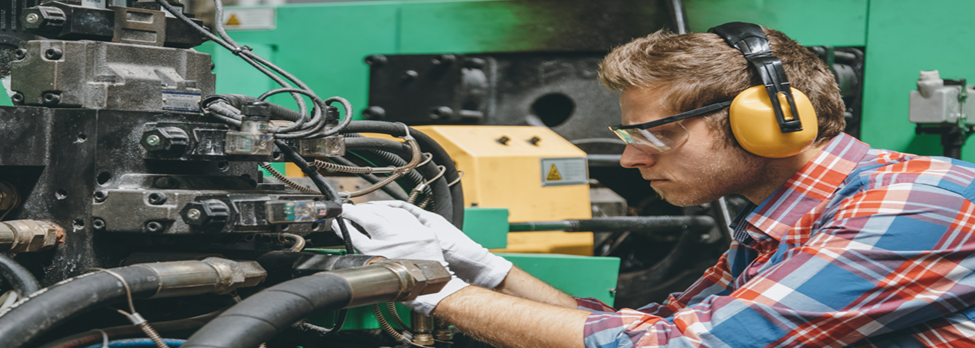
Proper installation of melt pressure transducers is critical to ensuring accurate pressure readings, prolonging sensor life, and maintaining efficient extrusion operations. Mistakes during installation can lead to inaccurate measurements, sensor damage, and costly downtime. This guide, developed in collaboration with the NoNonSensors Technical Sales Team, highlights the most common installation concerns and best practices for maintenance professionals.
1. Incorrect Mounting Depth
Issue: If the transducer is not installed at the correct depth, the sensor may be exposed to excessive pressure or fail to properly contact the melt stream.
Solution: Follow the manufacturer’s specifications for mounting depth. The diaphragm should be flush with the inner barrel wall to ensure accurate pressure measurement.
2. Improper Torque Application
Issue: Over-tightening can damage the sensor threads or diaphragm, while under-tightening can lead to leaks and inaccurate readings.
Solution: Use a torque wrench and apply the recommended torque value specified in the transducer’s installation manual.
3. Contaminant Build-up on the Diaphragm
Issue: Residual polymer or carbonized material on the sensor diaphragm can lead to false readings or complete failure.
Solution: Regularly clean the sensor with a non-abrasive cloth and approved cleaning agents. Avoid using metal tools that can scratch the diaphragm.
4. Improper Wiring and Electrical Interference
Issue: Incorrect wiring or exposure to electromagnetic interference (EMI) can cause erratic readings and signal loss.
Solution: Ensure proper wiring according to the sensor’s schematic. Use shielded cables and keep wiring away from high-power electrical components.
5. Overheating and Temperature Management
Issue: Excessive heat can damage the sensor electronics, causing drift or complete failure.
Solution: Verify that the transducer is rated for the extrusion temperature. If necessary, use cooling jackets or thermal barriers to protect the sensor.
6. Sensor Overpressure and Shock Loading
Issue: Pressure spikes or exceeding the sensor’s rated capacity can lead to premature failure.
Solution: Select a transducer with an appropriate pressure range and install a pressure relief mechanism if necessary.
7. Poor Sensor Alignment
Issue: Misalignment can cause pressure inconsistencies and mechanical stress on the sensor body.
Solution: Ensure that the mounting hole is correctly machined and aligned per manufacturer specifications.
8. Lack of Routine Calibration and Maintenance
Issue: Over time, sensors can drift, leading to inaccurate measurements and process inefficiencies.
Solution: Implement a regular calibration schedule using a pressure calibrator to verify and adjust sensor readings.
By addressing these common installation concerns, maintenance personnel can maximize the performance and lifespan of melt pressure transducers in extrusion applications. Proper installation, routine maintenance, and adherence to best practices will help ensure accurate pressure monitoring and reduce costly downtime.
For further technical assistance and product recommendations, contact the NoNonSensors Technical Sales Team today.
Comments